3D Printing Fashion Revolution: Insider Secrets from Underground Designers
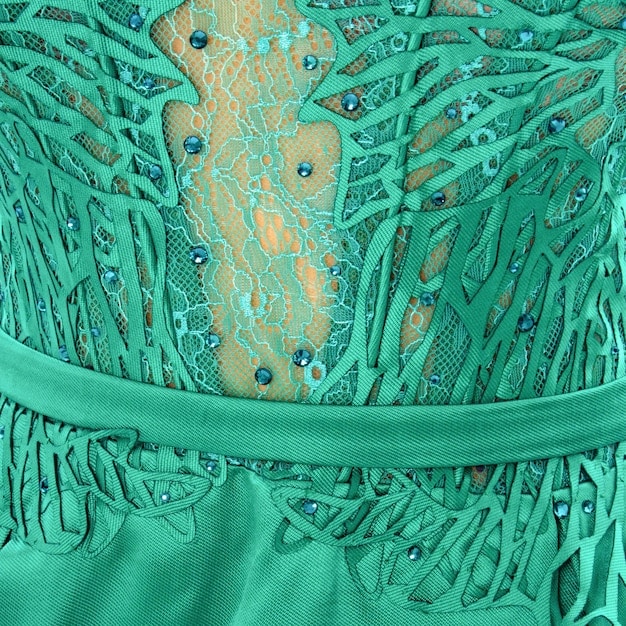
Underground designers are revolutionizing the fashion industry by leveraging 3D printing to create innovative, sustainable, and personalized garments, pushing the boundaries of traditional fashion design.
Discover the Insider Secrets: How Underground Designers are Using 3D Printing to Revolutionize Fashion, exploring the cutting-edge techniques and sustainable practices that are reshaping the industry from the bottom up.
The Rise of 3D Printing in Underground Fashion
3D printing is no longer a futuristic fantasy; it’s a tangible reality reshaping the fashion landscape. In the underground fashion scene, this technology offers unprecedented creative freedom and customization, empowering designers to push boundaries and redefine what’s possible.
The integration of 3D printing into fashion is creating ripples, offering sustainable alternatives, and personalized designs. It’s a shift that challenges traditional manufacturing processes and opens doors for independent creators to thrive.
Unleashing Creative Potential
One of the primary appeals of 3D printing for underground designers is its ability to bring intricate, avant-garde designs to life that would be nearly impossible with traditional methods.
Sustainable Fashion Practices
3D printing also supports sustainable practices by reducing waste and allowing for on-demand production, addressing some of the most pressing environmental concerns in the fashion industry.
- Customization and Personalization: 3D printing allows for highly customized designs, tailored to the individual’s body shape and preferences, offering a level of personalization previously unattainable.
- Material Innovation: Designers are experimenting with a range of materials, from flexible filaments to recycled plastics, creating unique textures and forms.
- Democratization of Design: 3D printing empowers independent designers by providing access to advanced manufacturing capabilities, leveling the playing field.
- Reducing Waste: The ability to print on-demand minimizes textile waste, a significant problem in traditional fashion production.
Ultimately, the rise of 3D printing in underground fashion is about more than just technology; it’s about fostering creativity, promoting sustainability, and empowering a new generation of designers to challenge the status quo.
Key Benefits of 3D Printing for Designers
3D printing offers an array of benefits for designers, particularly those operating outside the mainstream fashion industry. These advantages span from increased design flexibility to sustainable production methods, fundamentally changing how garments and accessories are conceived and created.
Understanding these core benefits is essential for appreciating the transformative impact of 3D printing on the fashion world. This technology not only streamlines processes but also encourages innovation and environmental responsibility.
Design Flexibility and Complexity
With 3D printing, designers can create complex geometries and intricate details that are difficult or impossible to achieve with traditional fashion techniques. This allows for greater artistic expression and innovation.
Rapid Prototyping and Iteration
3D printing enables designers to quickly prototype and test new ideas, reducing the time it takes to bring a concept to fruition. This rapid iteration process allows for more experimentation and refinement.
- Cost-Effectiveness: 3D printing can reduce production costs by eliminating the need for molds, tooling, and large-scale manufacturing setups.
- On-Demand Production: Designers can produce items only when they are needed, reducing inventory costs and waste.
- Material Efficiency: 3D printing uses only the material necessary to create an object, minimizing waste compared to traditional cutting and sewing methods.
- Sustainability: Using sustainable materials like recycled plastics in 3D printing further enhances its environmental benefits.
The benefits of 3D printing extend beyond just the creative process. It offers practical advantages that can help underground designers compete in a rapidly changing industry, making it a game-changing technology for fashion innovation.
Case Studies: Underground Designers Leading the Way
Several underground designers have already begun to harness the power of 3D printing, creating stunning and innovative pieces that are pushing the boundaries of fashion. These early adopters serve as inspiring examples of what can be achieved with this technology.
Their work not only showcases the creative potential of 3D printing but also highlights its ability to challenge traditional fashion norms. These case studies provide a glimpse into the future of fashion design.
XYZ Workshop: Functional Fashion
XYZ Workshop is known for creating functional 3D-printed fashion items, including shoes and accessories. Their designs focus on practicality and sustainability, demonstrating how 3D printing can be used to create everyday items.
Danit Peleg: Accessible Innovation
Danit Peleg gained recognition for 3D printing an entire fashion collection at home using affordable desktop printers. Her work highlights the accessibility of 3D printing and its potential to revolutionize personal fashion.
- Nervous System: This design studio combines science, mathematics, and art to create intricate 3D-printed jewelry and apparel, showcasing the complex designs possible with 3D printing.
- Julia Koerner: Koerner designs architectural and sculptural fashion pieces, often collaborating with high-profile brands and artists, demonstrating the versatility of 3D printing in high fashion.
- Travis Fitch: Fitch explores the intersection of fashion and technology, creating innovative 3D-printed textiles and garments that challenge traditional notions of clothing construction.
These designers are at the forefront of a movement that is transforming the fashion industry. By embracing 3D printing, they are not only creating unique and innovative pieces but also paving the way for a more sustainable and accessible future for fashion.
The Challenge of Scaling 3D-Printed Fashion
While 3D printing offers numerous advantages for underground designers, scaling production to meet broader market demands presents significant challenges. Overcoming these obstacles is crucial for the widespread adoption of 3D-printed fashion.
Addressing these challenges requires innovative solutions in material science, printing technology, and supply chain management. Despite these hurdles, the potential rewards of scaling 3D-printed fashion are substantial.
Material Limitations
The range of materials available for 3D printing in fashion is still somewhat limited compared to traditional textiles. Expanding the material options is essential for creating more diverse and functional garments.
Production Speed and Capacity
3D printing is generally slower than traditional manufacturing methods, making it difficult to produce large quantities of clothing quickly. Increasing printing speeds and capacity is a key area of development.
- Cost of Equipment: The initial investment in 3D printing equipment can be substantial, posing a barrier for small-scale designers and startups.
- Software and Skills: Designing for 3D printing requires specialized software skills, which can be a learning curve for designers accustomed to traditional methods.
- Durability and Comfort: Ensuring that 3D-printed garments are durable and comfortable to wear is crucial for consumer acceptance.
- Supply Chain Logistics: Establishing efficient supply chains for 3D-printed fashion requires new approaches to sourcing, production, and distribution.
Solving these challenges will require collaboration between designers, engineers, and material scientists. Investing in research and development is essential for unlocking the full potential of 3D-printed fashion and making it a viable option for a wider audience.
Sustainability and the Future of Fashion
One of the most compelling aspects of 3D printing in fashion is its potential to contribute to more sustainable practices. Traditional fashion production is notorious for its environmental impact, but 3D printing offers an alternative that can reduce waste and promote eco-friendly materials.
Exploring these sustainable opportunities is crucial for aligning the fashion industry with global environmental goals. 3D printing not only reduces waste but also encourages the use of innovative, sustainable materials.
Reducing Textile Waste
3D printing minimizes textile waste by using only the material necessary to create a garment. This contrasts sharply with traditional cutting and sewing methods, which often result in significant fabric scraps.
Using Sustainable Materials
Designers are increasingly experimenting with sustainable materials, such as recycled plastics and bio-based filaments, for 3D printing. This further reduces the environmental impact of fashion production.
- On-Demand Production: 3D printing enables on-demand production, eliminating the need for large inventories and reducing the risk of unsold items ending up in landfills.
- Localized Production: 3D printing can facilitate localized production, reducing the carbon footprint associated with shipping garments from overseas factories.
- Customization and Longevity: By creating customized garments that fit perfectly and last longer, 3D printing can reduce the need for frequent replacements.
- Closed-Loop Systems: 3D printing can support closed-loop systems, where used garments are recycled and repurposed into new materials for printing.
By embracing 3D printing, the fashion industry can take significant steps towards a more sustainable and responsible future. This technology offers a pathway to reducing waste, conserving resources, and creating garments that are both stylish and environmentally friendly.
How to Get Involved in 3D-Printed Fashion
For designers and fashion enthusiasts interested in exploring 3D-printed fashion, there are numerous ways to get involved. From learning the necessary skills to connecting with a community of like-minded individuals, the opportunities are vast and accessible.
Embarking on this journey requires a combination of education, experimentation, and networking. With the right resources and attitude, anyone can contribute to the exciting world of 3D-printed fashion.
Learning 3D Modeling and Printing
The first step is to acquire the skills necessary to design and print 3D garments. This includes learning 3D modeling software and understanding the basics of 3D printing technology.
Experimenting with Materials and Techniques
Once you have the basics down, it’s time to start experimenting with different materials and printing techniques. This hands-on experience is crucial for developing your own unique style and approach.
- Taking Online Courses: Numerous online platforms offer courses on 3D modeling, printing, and fashion design, providing a structured learning experience.
- Attending Workshops and Conferences: Workshops and conferences provide opportunities to learn from experts, network with other designers, and see the latest innovations in 3D-printed fashion.
- Joining Online Communities: Online communities, such as forums and social media groups, can provide support, feedback, and inspiration.
- Collaborating with Other Designers: Collaborating with other designers can help you learn new skills, share resources, and create more innovative and impactful projects.
By taking these steps, you can immerse yourself in the world of 3D-printed fashion and contribute to its continued growth and innovation. The possibilities are endless, and the future of fashion is waiting to be shaped.
Key Point | Brief Description |
---|---|
💡 Creative Freedom | 3D printing allows complex, avant-garde designs. |
♻️ Sustainability | Reduces waste through on-demand production. |
🚀 Rapid Prototyping | Enables quick testing and iteration of designs. |
🛠️ Customization | Offers highly personalized garments. |
Frequently Asked Questions
▼
3D printing offers increased design flexibility, rapid prototyping, cost-effectiveness, and sustainable production methods, allowing designers to create intricate and personalized garments while reducing waste.
▼
It minimizes textile waste by using only the necessary material, supports on-demand production, and encourages the use of sustainable materials like recycled plastics, reducing the environmental impact.
▼
Challenges include material limitations, slower production speeds, the high cost of equipment, the need for specialized skills, and ensuring the durability and comfort of 3D-printed garments.
▼
Notable designers include XYZ Workshop, known for functional fashion; Danit Peleg, who 3D-printed an entire collection at home; and Nervous System, which creates intricate jewelry and apparel.
▼
You can get involved by learning 3D modeling and printing, experimenting with materials, taking online courses, attending workshops, and joining online communities to connect with other designers.
Conclusion
As we’ve explored, underground designers are at the vanguard of a fashion revolution, leveraging 3D printing to create innovative, sustainable, and personalized garments. While challenges remain in scaling production and expanding material options, the benefits of reduced waste, increased design flexibility, and on-demand production make 3D printing a game-changing technology for the future of fashion. By embracing this technology, designers can push the boundaries of creativity and help build a more sustainable and accessible fashion industry.