3D Printing Revolution: Underground Designers Reshaping Fashion
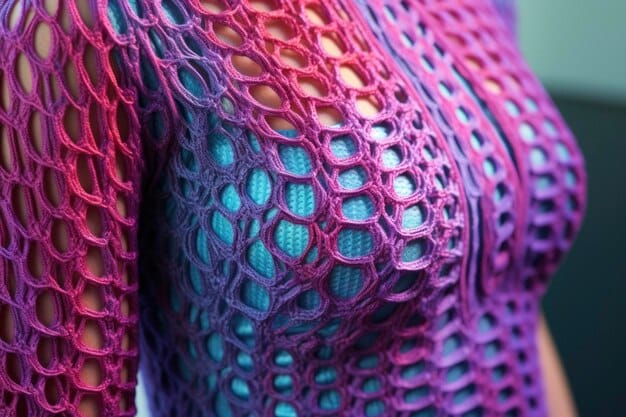
Insider Secrets: How Underground Designers are Using 3D Printing to Revolutionize Fashion reveals how cutting-edge creatives are leveraging additive manufacturing to personalize designs, innovate materials, and disrupt traditional fashion industry norms.
The world of fashion is constantly evolving, and one of the most exciting developments is the use of 3D printing by underground designers. Insider Secrets: How Underground Designers are Using 3D Printing to Revolutionize Fashion uncovers how these innovators are pushing boundaries and shaping the future of wearable art.
The Rise of 3D Printing in Underground Fashion
3D printing, once a technology confined to industrial applications, has now found a vibrant home in the underground fashion scene. Underground designers are seeing it as an innovative tool, not just a trend.
This innovative technology is enabling designers to bring to life concepts that were previously impossible, marking a shift towards greater customization and creativity. By integrating 3D printing, they’re breaking molds and making waves.
What is 3D Printing and Why Fashion?
3D printing, also known as additive manufacturing, involves building three-dimensional objects layer by layer from a digital design. The materials utilized vary, with each having their own impact.
In fashion, this technology offers unparalleled design freedom, allowing creators to produce complex shapes and intricate details with relative ease. It has provided an all new means of creating custom pieces.
- Unlimited Customization: Designers can tailor garments to individual body types, creating perfectly fitted clothing.
- Complex Designs: Intricate patterns and shapes can be realized without the limitations of traditional manufacturing.
- Sustainable Practices: 3D printing reduces material waste, as only the necessary material is used in production.
- Rapid Prototyping: Designers can quickly iterate on designs, speeding up the creative process.
The rise of 3D printing in underground fashion signifies a new era of personalized, sustainable, and inventive clothing design. It is also changing how we look at clothing.
The Designers Leading the 3D Printing Charge
Several underground designers are at the forefront of this revolution, each with their unique vision and approach. They are developing new styles using this one of a kind technology.
These visionaries are not just adopting 3D printing; they are mastering it and pushing its capabilities to create garments that are both art and technology. Their stories highlight the power of innovation in fashion, something that they have been doing for years.
Pioneering Designers and Their Creations
From avant-garde dresses to futuristic accessories, these designers are showcasing the versatility of 3D printing. Underground designers are also showing the world that 3D printing can be sustainable.
Their collections often incorporate unusual materials and groundbreaking techniques, challenging conventional notions of what clothing can be. It isn’t just about the clothing, but about the expression.
- Iris van Herpen: Known for her sculptural dresses and collaborations with architects, van Herpen combines technology with haute couture. She truly is a visionary.
- Neri Oxman: An architect and designer at MIT Media Lab, Oxman creates intricate pieces inspired by nature, exploring the intersection of biology and design.
- Danit Peleg: Peleg is known for her fully 3D-printed fashion collections, emphasizing open-source designs and sustainable practices.
These designers and others like them are actively shaping the future of fashion, proving that creativity knows no bounds when combined with technology. Each designer uses the technology to make new creations.
Materials and Technologies Shaping the Future
The materials used in 3D printing are just as crucial as the designs themselves. Designers are always trying to push the boundaries of materials.
New innovations in materials technology are continuously expanding the possibilities for 3D-printed fashion, making garments more flexible, durable, and sustainable. Each new material will lead to new ways of doing 3D printing.
Advancements in 3D Printing Materials
From flexible filaments to sustainable bio-plastics, the range of materials available is rapidly growing. By using new materials, it is giving designers and all new range of creative choices.
These materials allow designers to create clothing that is not only visually stunning but also comfortable and functional. These materials can also be very environmentally friendly.
- TPU (Thermoplastic Polyurethane): A flexible and durable material ideal for creating wearable garments that move with the body.
- PLA (Polylactic Acid): A bio-plastic made from renewable resources, offering a sustainable alternative to traditional plastics.
- Nylon: A strong and lightweight material suitable for creating robust and long-lasting fashion pieces.
The integration of these materials is redefining the possibilities for 3D-printed fashion, driving innovation and sustainability in the industry. Sustainability really is making things much more viable.
Sustainability and Ethical Considerations
One of the most compelling aspects of 3D printing is its potential to promote sustainability in fashion. Sustainability is the driving force behind the innovation.
By reducing waste and enabling on-demand production, 3D printing offers a more environmentally friendly approach to clothing manufacturing. It is also making designers more conscious overall.
The Environmental Benefits of 3D Printing
Traditional fashion manufacturing is notorious for its environmental impact, from water pollution to textile waste. However, this issue has been diminishing.
3D printing addresses many of these concerns by minimizing waste, reducing the need for mass production, and enabling the use of sustainable materials. Sustainable practices are making the entire field better.
Reduced Waste: 3D printing uses only the necessary material, minimizing textile waste and reducing the environmental footprint.
On-Demand Production: Clothing can be produced as needed, avoiding overproduction and reducing the need for large inventories.
Sustainable Materials: The use of bio-plastics and other sustainable materials further minimizes the environmental impact of fashion manufacturing.
The shift towards sustainable practices is essential for the future of fashion, and 3D printing offers a promising path forward. Fashion may have a green future yet!
Challenges and Opportunities in 3D-Printed Fashion
While 3D printing offers numerous advantages, it also presents unique challenges for designers. With these challenges, comes new opportunities.
Overcoming these obstacles will be crucial for the widespread adoption of 3D printing in the fashion industry, paving the way for new creative possibilities. With widespread adoption, the opportunities will be limitless.
- Material Limitations: The range of materials suitable for 3D-printed fashion is still limited compared to traditional textiles.
- Scalability: Scaling up production to meet consumer demand remains a challenge for 3D-printed fashion.
- Cost: The cost of 3D printing equipment and materials can be prohibitive for some designers.
Despite these challenges, the opportunities are vast. As technology advances and costs decrease, 3D printing will become more accessible, transforming the way we design, manufacture, and consume fashion. As technology changes, anything is possible.
The Future of 3D Printing in Fashion
Looking ahead, the future of 3D printing in fashion is bright. It may become one of the most dominant forms of design.
As technology continues to evolve and designers push the boundaries of what’s possible, 3D printing will play an increasingly important role in shaping the fashion landscape. This technology may just dominate the world in the future.
Predictions and Trends
From personalized clothing to on-demand manufacturing, 3D printing is set to revolutionize every aspect of the fashion industry. We may be getting close to the Jetsons age of fashion.
Here are some key trends and predictions for the future:
Mass Customization: 3D printing will enable brands to offer personalized clothing tailored to individual body types and preferences.
On-Demand Manufacturing: Consumers will be able to order custom-designed clothing that is printed and delivered within days.
Sustainable Fashion: 3D printing will promote sustainable practices by reducing waste and enabling the use of eco-friendly materials.
As 3D printing becomes more integrated into the fashion industry, we can expect to see even more innovative and sustainable designs. Technology is our friend, not our enemy.
Key Point | Brief Description |
---|---|
💡 Customization | Enables personalized fashion designs tailored to individual preferences. |
🌱 Sustainability | Reduces waste, promotes on-demand production, and utilizes eco-friendly materials. |
🚀 Innovation | Drives new designs, materials, and production methods in the fashion industry. |
⚙️ Technology | Advances offer new possibilities and overcome challenges in 3D printed fashion. |
FAQ
▼
3D printing in fashion involves creating garments and accessories layer by layer from digital designs using materials like flexible plastics and sustainable bio-plastics. This allows for intricate, custom designs.
▼
3D printing reduces waste by only using the necessary materials, enabling on-demand production to avoid overstock, and facilitating the use of eco-friendly materials, promoting sustainable fashion practices.
▼
Key designers include Iris van Herpen, known for sculptural dresses; Neri Oxman, exploring biology and design; and Danit Peleg, focusing on open-source, fully 3D-printed fashion collections.
▼
Common materials include TPU (flexible and durable), PLA (sustainable bio-plastic), and Nylon (strong and lightweight), allowing for a range of textures and functionalities in 3D printed garments.
▼
Challenges include material limitations, scalability issues for mass production, and the high costs of 3D printing equipment and materials, which can hinder widespread adoption in the fashion industry.
Conclusion
The integration of 3D printing into underground fashion is more than just a technological advancement; it represents a fundamental shift in how we approach design, production, and consumption. As more designers embrace this technology, we can expect to see even more groundbreaking creations that challenge conventions and push the boundaries of what fashion can be, ultimately creating a more sustainable and personalized industry.